La Vallée des Élastomères commissioned the CTTÉI to map elastomer residues in Quebec and identify higher value-added recovery solutions.
A fruitful collaboration
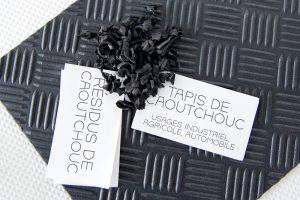
In 2013, the CTTÉI had already carried out a " Study for the development of rubber residues " for the Vallée des Élastomères, a cluster of expertise bringing together nearly 30 companies, supported by the Ministère de l'Économie, de l'Innovation et de l'Énergie to support innovation, development and circularity in the sector.
Michel Rousseau, director of the niche, commissioned the CTTÉI in 2023 to update knowledge and study ways of improving value-added.
In 2023, the CTTÉI carried out the following work:
- Mapping of elastomer residues based on data from Vallée des Élastomères members in Quebec (September 2023)
- Identification of valorization solutions (December 2023):
- Review of circular economy technologies and practices in Quebec and internationally with regard to the valorization of rubber residues
- Identification of valorization solutions
- Prioritization and selection of 5 circular economy scenarios to be developed in Quebec.
In all, over 70 practices were inventoried and over 100 technical documents from a variety of reliable sources were used. Conducted in collaboration with the members of Vallée des Élastomères, they also benefited from the assistance of circular economy facilitators from the Synergie Québec community of practices, Quebec's network of industrial and territorial symbioses.
High value-added potential
Several lessons have been learned from the work undertaken:
- The efforts made with end-of-life tires should be extended to the treatment of all elastomer residues in Quebec. Although the majority of elastomer residues are recycled externally (4,911 t/year) or recovered for energy purposes (1,249 t/year), a significant proportion (5,302 t/year) is currently destined for technical landfill sites.
- Because of the diversity of elastomers found among industrial residues, recycling by an isolated company is difficult. Current production processes are specific to each plant and designed to use virgin raw materials. Pooling the resources and efforts of industry players is therefore a key factor in improving practices.
- Adopting an approach based on the properties of blends rather than on specific recipes would simplify raw materials management and enable the integration of recycled materials.
- New technologies are available today to valorize elastomers in outlets with higher economic value. Indeed, the majority of current recovery cycles can be described as under-cycling, whereas better options exist.
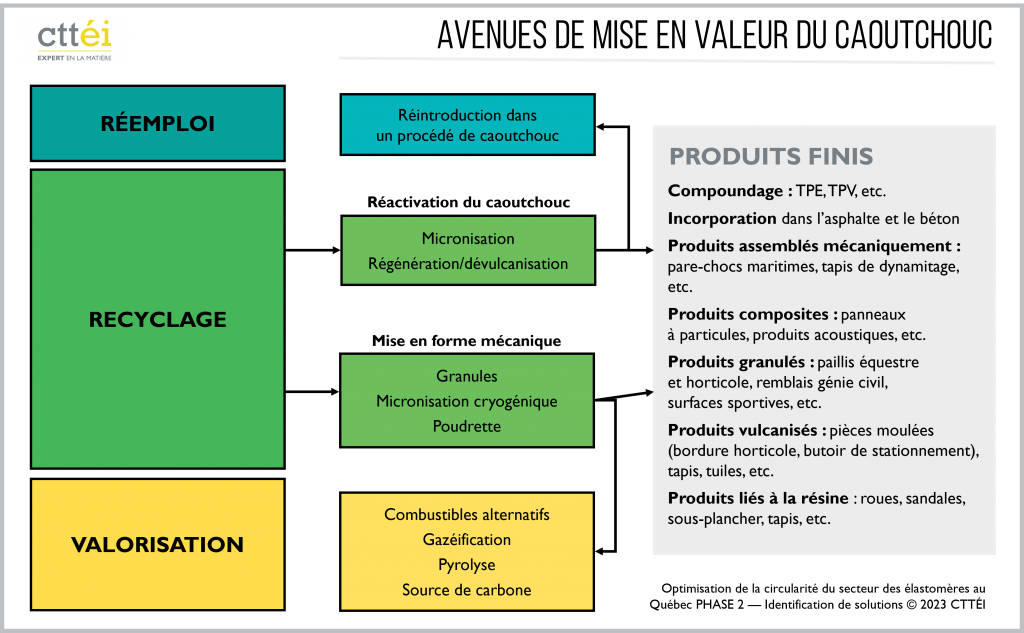
Promising new processes include :
- Devulcanization, cryogenics and pyrolysis are techniques that could make it possible to manufacture value-added products. Take, for example, a devulcanization process that produces a non-virgin raw material that is more competitive than virgin material: the purchase cost of revalorized granulated rubber is around 800 Canadian dollars per tonne, whereas virgin rubber costs between 2,600 and 3,400 Canadian dollars per tonne (Levgum process, Israel).
- Theuse of powders in the manufacture of new tires, bitumen or composite mixes incorporating plastic remains an interesting option.
- Energy recovery in cement plants can also be used as a last resort, in line with the 3RV hierarchy.
The five desirable scenarios identified now need to be studied in greater depth by a technical-economic study: CAPEX-OPEX, quantification of environmental gains and benefits (including a GHG balance), modeling of residual material flows, etc.
Thanks to the work carried out together in 2023, Vallée des Élastomères and its members are in a position to take enlightened action to divert rubber residues from landfill, in a circular economy perspective.
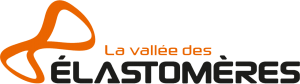